Johann Schild GmbH Uses FSM to Modernize Service Operations
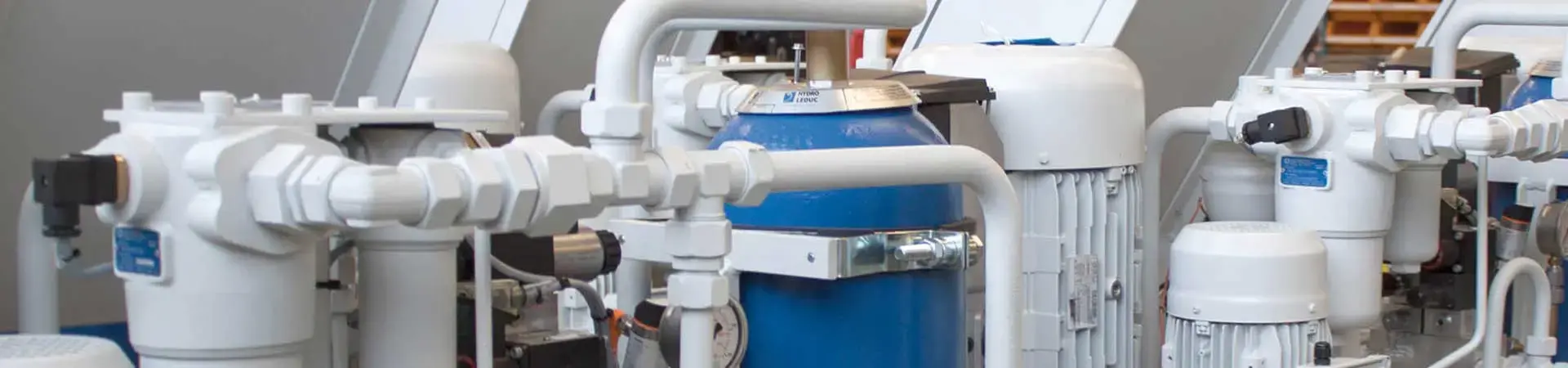
Johann Schild Sr. began his career in the agricultural sector before he turned his hobby – technology – into a career. Since then, the company has grown from a two-man operation into a medium-sized traditional company. After almost 30 years in business, his son Johann Schild Jr. (who is also the current Managing Director) decided to take the path of innovation rather than stick with the traditional time clock.
Since the employees work in manufacturing as well as service, one requirement for this change that was faced by the software company, Coresystems, was to implement a time-recording system that would be as flexible as possible. Until this point, service employees had to come into the office in order to have their card read by the time clock. That cost time and money. The time recording had gaps in it if staff lost their time cards.
"One of the most important points for us was that the system had to be mobile, i.e. the employees are not tied to a specific location to work with the system," explains the Managing Director, Johann Schild.
The company had already introduced SAP Business One as their ERP system, along with the enhancements from Coresystems. The mobile field staff solution and the time-recording system therefore had to be connected to the ERP system. It was also important to Johann Schild that the product had already been used successfully on the market. Schild was pleased with the Coresuite Country Package products that had already been introduced. So, it was a logical step to integrate time recording with Coresuite Time, along with the mobile Field Service Software. The company’s requirements at a glance:
- Flexible time-recording system
- Integration into the SAP Business One ERP system
- Market-tested product
The system was implemented quickly and without any problems. “Right from the start, we were able to work just the way we had envisaged,” confirms Schild.
However, the full scope of the solution only became clear once the company had started to use it. When they are on a job, service engineers can now access all of the data on-site and pass this onto the customer. They also know exactly what work their predecessor has carried out on the machine up until that point and for how long their colleague worked. In addition, other departments (such as Controlling) or management also have all of the data at their fingertips at all times. With this solution, the company has created an end-to-end business process. From creating the quotation, project planning, production and commissioning, right through to service work – the SAP Field Service Software is used in every phase of the process.
We can say that the business process works significantly faster for us than it used to and, most importantly, it works without errors. And that is the bottom line. - Johann Schild Jun., Managing Director
As a result, the time between the service work and issuing the invoice has also been reduced. Service staff can now use their mobile devices to create the invoices and delivery notes at the touch of a button. "Of course, we have now become significantly faster at evaluating the times and therefore issuing invoices, and much quicker at carrying out post-calculation work," says Schild.
And Schild's customers are satisfied too – the system impresses them with its innovation and transparency. The customer knows the history of the product and can access detailed reports and invoices for the services rendered.
About Johann Schild Herstellung & Handels GmbH
In 1987, Johann Schild Senior founded the family business, Schild Herstellung & Handels GmbH, as a small technical retailer. Since then, the company has grown to become a single- source supplier for hydraulic systems and accessories.
It employs around 45 members of staff that design and manufacture hydraulic systems for the automotive, packaging and disposal industries. If requested by the customer, the company also commissions and services the devices.